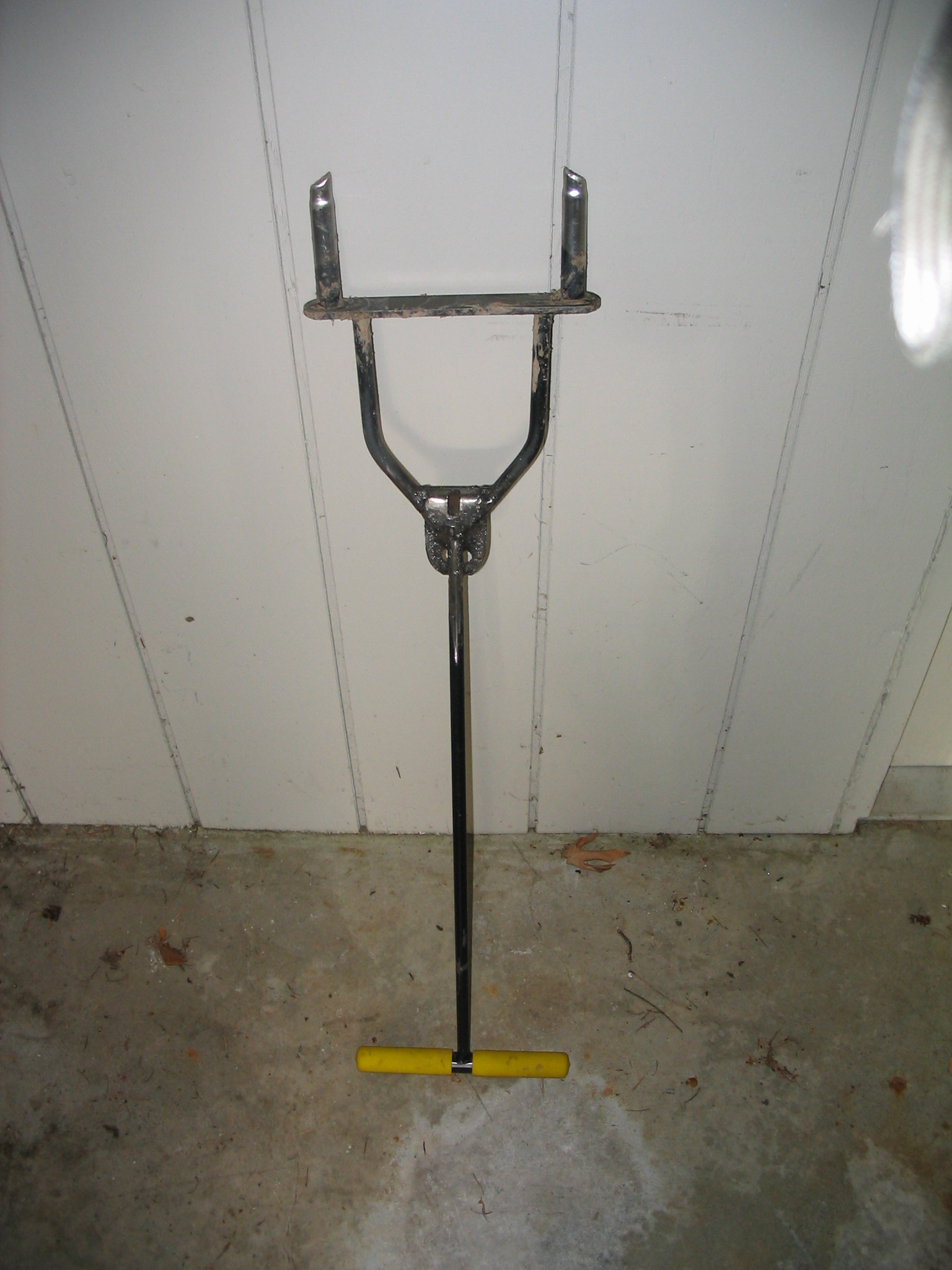
The handle broke off my manual lawn aerator. It had been welded in place, and since I have an arc welder, I figured I should weld it back on. This was the first time I attempted to arc weld something with a real purpose to it. There were a few details to work out, such as the fact that I don’t know if the welder works right, and I don’t know if my welding rods are any good, and what was the other one? Oh yeah, I don’t know how to arc weld. Well OK then, time to get started.
Actually, I do know the arc welder works, at least nominally. I got the arc welder from my friend Tim when he got a better one. It is your typical “stick” AC arc welder, with no fancy features. He used it at least once. I think. It’s a solidly-built big old monster with a giant transformer inside and a hand crank to turn the amperage up or down. The amperage indicator needle was missing; I replaced it but don’t know how close it reads to reality. My dad helped me make a few practice welds with it last year, so someone who knows what they are doing should be able to make it work. Ahem.
I got the welding rods from my dad, who had a bunch of these sticks left over from his previous job. I’ve heard you have to keep them dry and in good condition for them to work right. They’ve been inside in a plastic bag to keep them dry, and they don’t look obviously bad to me. That’s pretty easy since I don’t know what a bad welding stick looks like.
Then there’s that knowing-what-you-are-doing part. I did some oxy-acetylene welding back in the dark ages, I mean the 1980’s, but not arc welding. So last year when I got this beast from Tim I figured I should learn a little and read up in I Can Do It All By Myself: My So-Big Book of Arc Welding or maybe it was called Introduction to Arc Welding, I forget which.
My dad bought me a cool welding helmet which automatically darkens in bright light and lightens again in normal light. If you don’t know what you are doing, it really helps if you can see it. I think.
I did read up on the safety stuff, and made sure to wear boots, long sleeves, and thicker denim jeans, along with proper welding gloves. Hot molten metal, no matter how small a splat, is not fun to feel. I also turned on a big box fan right next to the work, because these fumes stink! Oh, and they’re toxic too, I hear.
I put some protection around to keep the splattering metal from flying onto everything else. (Don’t weld over a pile of sawdust.) When I first tested the welder last year, we set up a shield using cement backer board, the kind you use as an under-surface for tile counters. This time I used some scraps of “HardieBacker”, which has cement in it but is a little more like sheetrock, so it is easier to cut and shape. Works great for a welding shield. And for laying tile, too.
So it was time to melt metal with fire using a blazing lightning bolt of electricity. Can you do anything cooler than that? Of course not. I figured I should do some practice welds on a piece of junk steel before mangling the lawn aerator. I grabbed some scraps from a discarded bed frame (awesome source of free angle iron) and set to work. I spent a long time getting the rod stuck to the piece, over and over, without getting an arc. Clearly I was not getting this arc thing figured out right.
I gave up after half an hour. Something wasn’t right. Either the welder was bad, the rods were bad, or I didn’t know what I was doing. Hmm. It could be any of the three, so I went into standard cheapskate troubleshooting mode: which of these variables can I improve or eliminate for almost no time or money? Buying another welder would not be cheap, unless I wanted to take forever, so that was out. Despite being the highest probability culprit, learning how to weld properly was not going to happen within the weekend, and would likely require known-good equipment, so that was out too.
Fortunately, a box of arc welding sticks was only ten dollars at the big orange home improvement store, and they were open. With new rods in hand (or rather a new one in the electrode holder), I had an arc and an acceptable weld on my test piece within a few minutes. The new rods were smaller than the ones I already had, and the box had a recommended amperage range for them which worked fairly well. That makes me think that the old rods may not have been bad; I just may have been using them with the wrong amperage setting. There’s that know-what-you’re-doing thing again; curses!
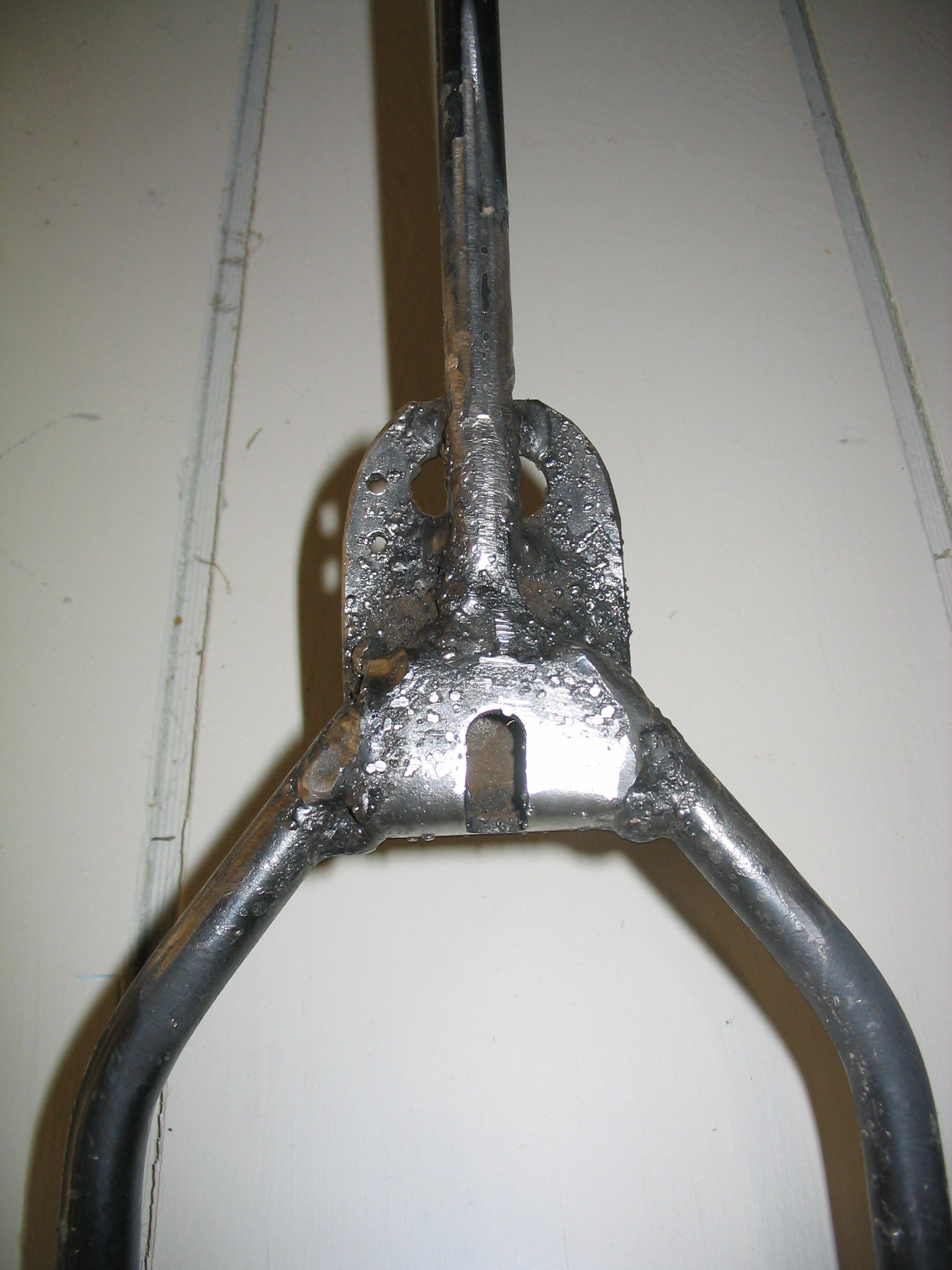
I cleaned up the broken parts of the lawn aerator on the grinding wheel to make a clean face and bevel the edges. After all the prior drama, it actually welded pretty easily. I also added a steel bracket to the joint, to reinforce it. I don’t know whether my new weld in the joint itself is a strong as the original factory weld (probably not), but I expect that the new bracket makes the whole thing stronger than before.
Once it was welded, I cleaned it up with the grinder and a wire-wheel brush on the electric drill. Success. I finished aerating the lawn, and it worked just fine. I melted metal using a white-hot electric arc, and I did it without burning down the house or injuring myself. You can’t beat that.